Preparing for Peak Shipping Seasons: Tips for Freight Efficiency
Understanding Peak Shipping Seasons
Every year, businesses brace themselves for peak shipping seasons, typically occurring during major holidays and events like Black Friday, Cyber Monday, and Christmas. These periods often lead to increased demand, putting significant pressure on logistics and supply chains. Preparing for these times is crucial to maintaining customer satisfaction and operational efficiency.
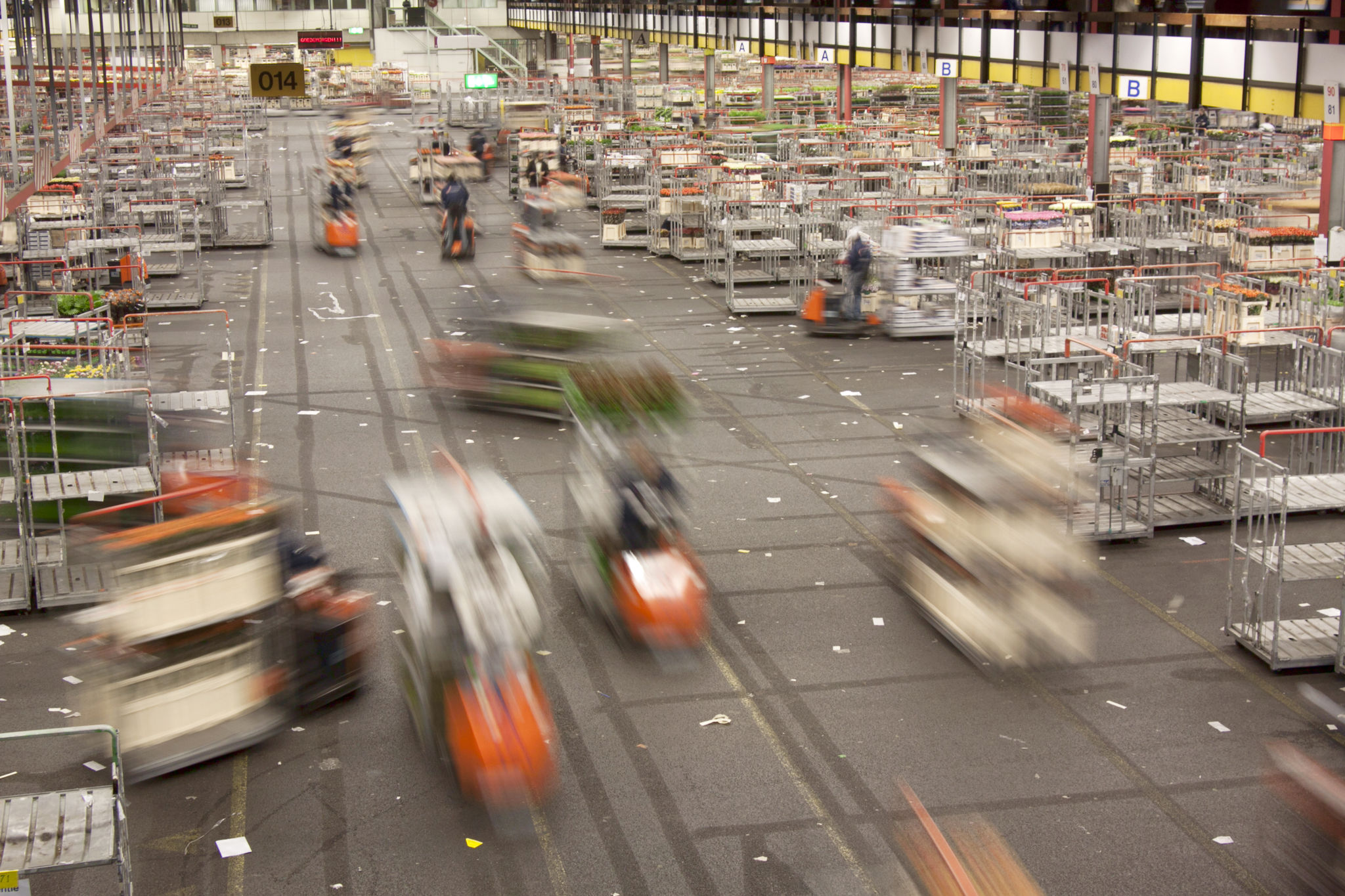
Peak shipping seasons can vary depending on the industry and geographic location. Companies need to recognize their specific peak times and plan accordingly. Understanding these patterns is the first step in effectively managing freight operations during busy periods.
Enhance Forecasting and Planning
Accurate forecasting is essential for preparing for peak shipping seasons. By analyzing historical data and trends, businesses can predict demand surges more effectively. This information helps in planning inventory levels, staffing, and transportation needs.
Collaborate with your supply chain partners to ensure everyone is aligned and prepared for the peak season. Regular meetings and communication can help identify potential bottlenecks and streamline operations.
Optimize Your Warehouse Operations
Efficient warehouse operations are critical during peak times. Consider reorganizing your warehouse layout to improve the flow of goods and reduce handling times. Employ technology like warehouse management systems (WMS) to track inventory in real-time and optimize storage space.
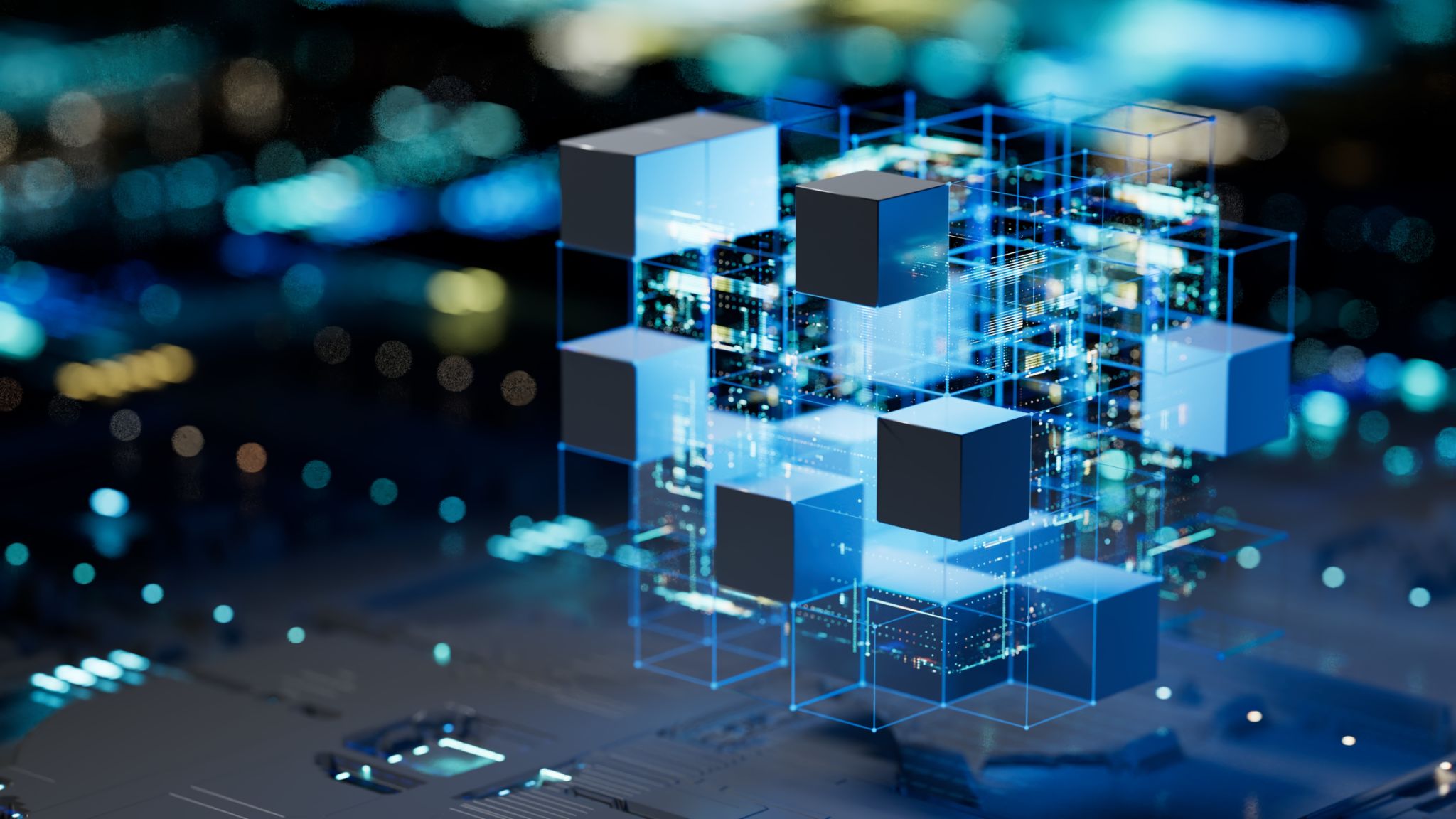
Additionally, training staff on efficient picking, packing, and shipping processes can lead to significant time savings. Temporary staffing solutions might also be necessary to manage the increased workload effectively.
Leverage Technology for Better Efficiency
Investing in technology can significantly enhance freight efficiency during peak seasons. Utilize tools such as route optimization software to minimize delivery times and fuel costs. Implementing tracking systems can also provide real-time updates, enhancing transparency and customer satisfaction.
Automation is another powerful tool to consider. Automated sorting and packing systems can speed up operations, reduce errors, and alleviate the pressure on human resources during busy periods.
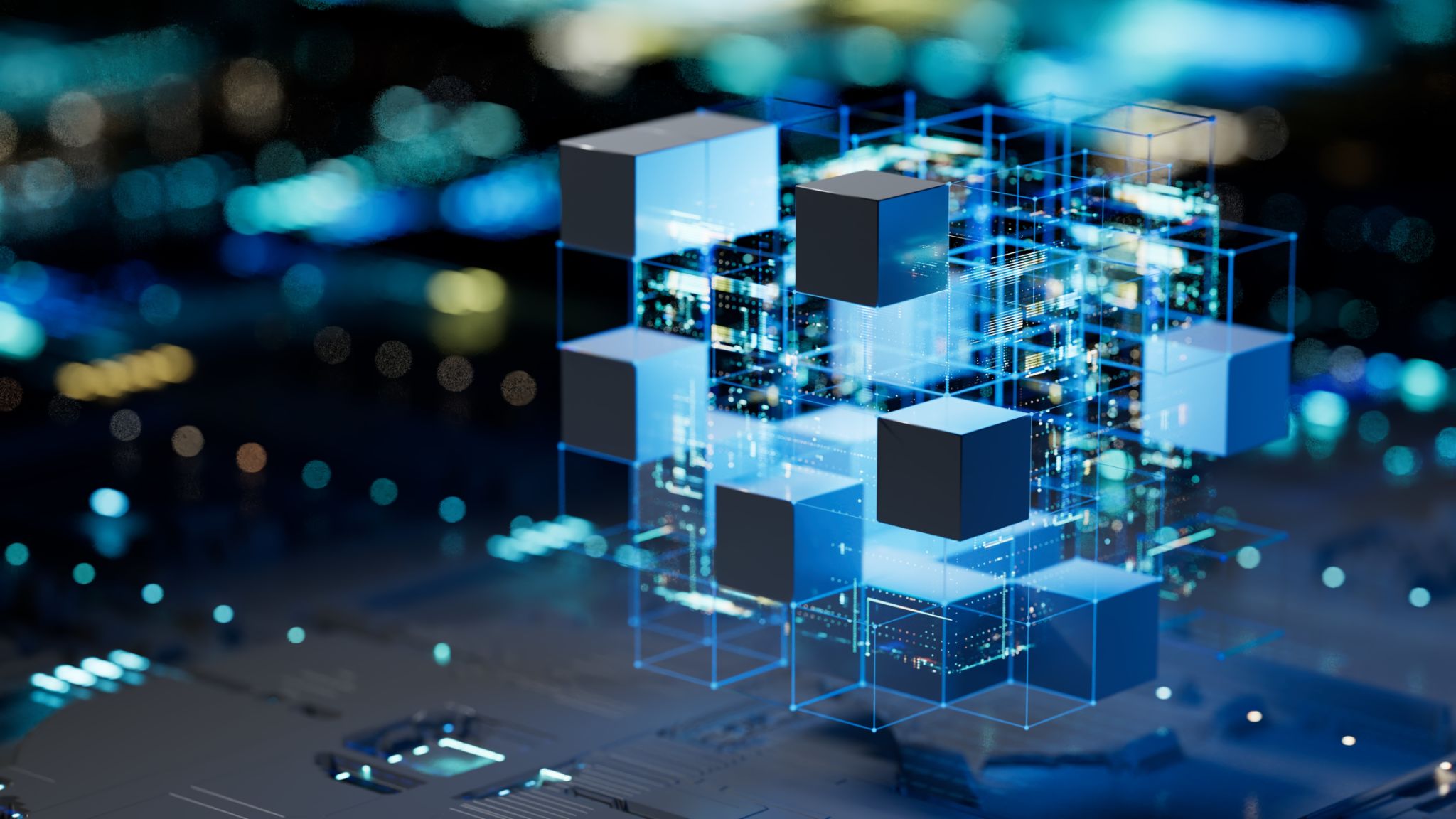
Build Strong Relationships with Carriers
Establishing strong relationships with carriers is vital for securing the capacity you need during peak times. Regular communication and long-term partnerships can lead to better service agreements and priority status in times of high demand.
Consider diversifying your carrier network to ensure flexibility. Having multiple carrier options can help mitigate risks associated with delays or capacity shortages.
Implement a Contingency Plan
No matter how well you prepare, unforeseen challenges can arise during peak shipping seasons. Having a robust contingency plan in place ensures your business can respond quickly to disruptions. This plan should include alternative routes, backup suppliers, and flexible staffing arrangements.
Regularly test and update your contingency plans to ensure they remain effective and relevant to current business conditions.
Monitor Performance and Gather Feedback
After the peak season concludes, take the time to analyze performance metrics such as delivery times, customer satisfaction, and cost efficiency. Gathering feedback from customers and employees can provide valuable insights into areas for improvement.
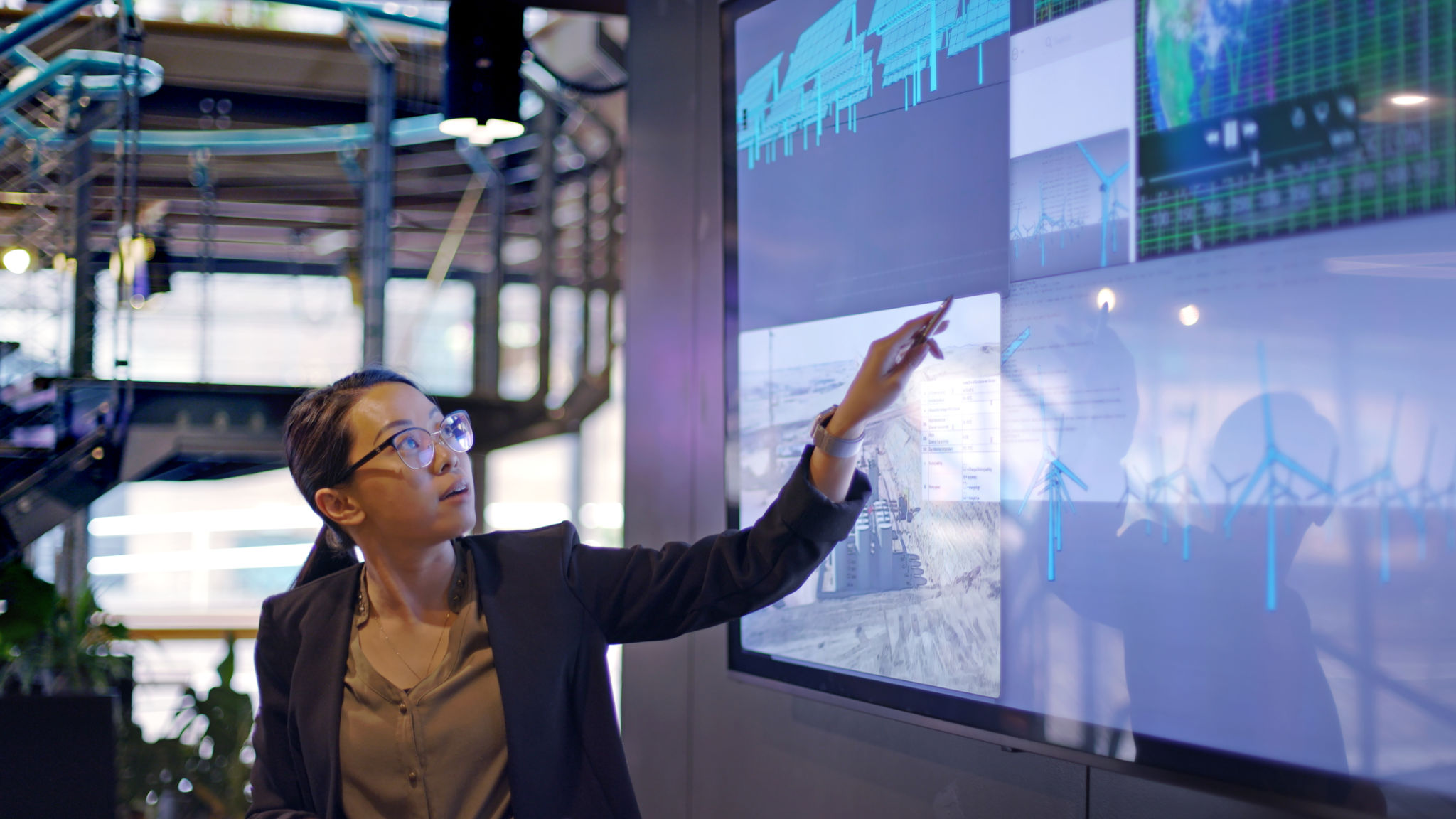
Use this data to refine your strategies for future peak periods, ensuring continuous improvement in freight efficiency and customer service.
Conclusion
Preparing for peak shipping seasons requires careful planning, collaboration, and investment in technology. By understanding demand patterns, optimizing operations, building strong partnerships, and having contingency plans in place, businesses can navigate these challenges successfully. Embrace these strategies to maintain freight efficiency and deliver outstanding service even during the busiest times of the year.